What is Porosity in Welding: Understanding Its Reasons and Enhancing Your Abilities
What is Porosity in Welding: Understanding Its Reasons and Enhancing Your Abilities
Blog Article
Porosity in Welding: Identifying Common Issues and Implementing Finest Practices for Avoidance
Porosity in welding is a pervasive problem that frequently goes undetected up until it triggers substantial troubles with the honesty of welds. In this discussion, we will check out the key aspects contributing to porosity formation, analyze its detrimental impacts on weld efficiency, and discuss the finest techniques that can be adopted to minimize porosity incident in welding procedures.
Common Reasons For Porosity

Making use of unclean or damp filler materials can present pollutants into the weld, contributing to porosity issues. To mitigate these common reasons of porosity, complete cleaning of base steels, appropriate shielding gas option, and adherence to ideal welding parameters are crucial methods in accomplishing premium, porosity-free welds.
Effect of Porosity on Weld High Quality

The existence of porosity in welding can significantly endanger the structural honesty and mechanical residential or commercial properties of bonded joints. Porosity develops gaps within the weld metal, weakening its general strength and load-bearing ability.
One of the key repercussions of porosity is a decline in the weld's ductility and durability. Welds with high porosity degrees often tend to show lower impact toughness and reduced capability to deform plastically prior to fracturing. This can be specifically concerning in applications where the bonded components go through vibrant or cyclic loading conditions. Porosity can hamper the weld's ability to effectively transmit pressures, leading to early weld failing and potential safety dangers in critical structures. What is Porosity.
Finest Practices for Porosity Prevention
To boost the architectural stability and top quality of bonded joints, what details measures can be implemented to reduce the incident of porosity during the welding process? Porosity prevention in welding is important to make sure the integrity and toughness of the final weld. One effective practice appertains cleaning of the base metal, removing any impurities such as rust, oil, paint, or dampness that might lead to gas entrapment. Making certain that the welding devices is in great condition, with tidy consumables and appropriate gas circulation rates, can additionally substantially decrease porosity. In addition, maintaining a secure arc and controlling the welding criteria, such as voltage, current, and take a trip speed, assists create a constant weld swimming pool that reduces the threat of gas entrapment. Utilizing the proper welding technique for the certain material being welded, such as readjusting the welding angle and gun setting, can better avoid porosity. Normal evaluation of welds and instant resource removal of any concerns identified during the welding procedure are essential methods to stop porosity and produce top notch welds.
Relevance of Appropriate Welding Methods
Carrying out appropriate welding methods is vital in making sure the architectural stability and high quality of welded joints, building on the foundation of reliable porosity avoidance measures. Welding methods straight influence the overall stamina and longevity of the welded structure. One essential aspect of proper welding strategies is keeping the proper heat input. Excessive warm can cause raised porosity as a result of the entrapment of gases in the weld pool. Conversely, inadequate warm may result in insufficient combination, creating prospective powerlessness in the joint. In addition, making use of the appropriate welding parameters, such as voltage, current, and travel speed, is essential for accomplishing sound welds with minimal porosity.
In addition, the choice of welding procedure, whether it be MIG, TIG, or stick welding, should line up with the details requirements of the job to guarantee optimal outcomes. Appropriate cleaning and prep work of the base metal, as well their explanation as choosing the right filler material, are likewise vital components of skilled welding methods. By adhering to these ideal practices, welders can lessen the threat of porosity formation and review generate top notch, structurally sound welds.
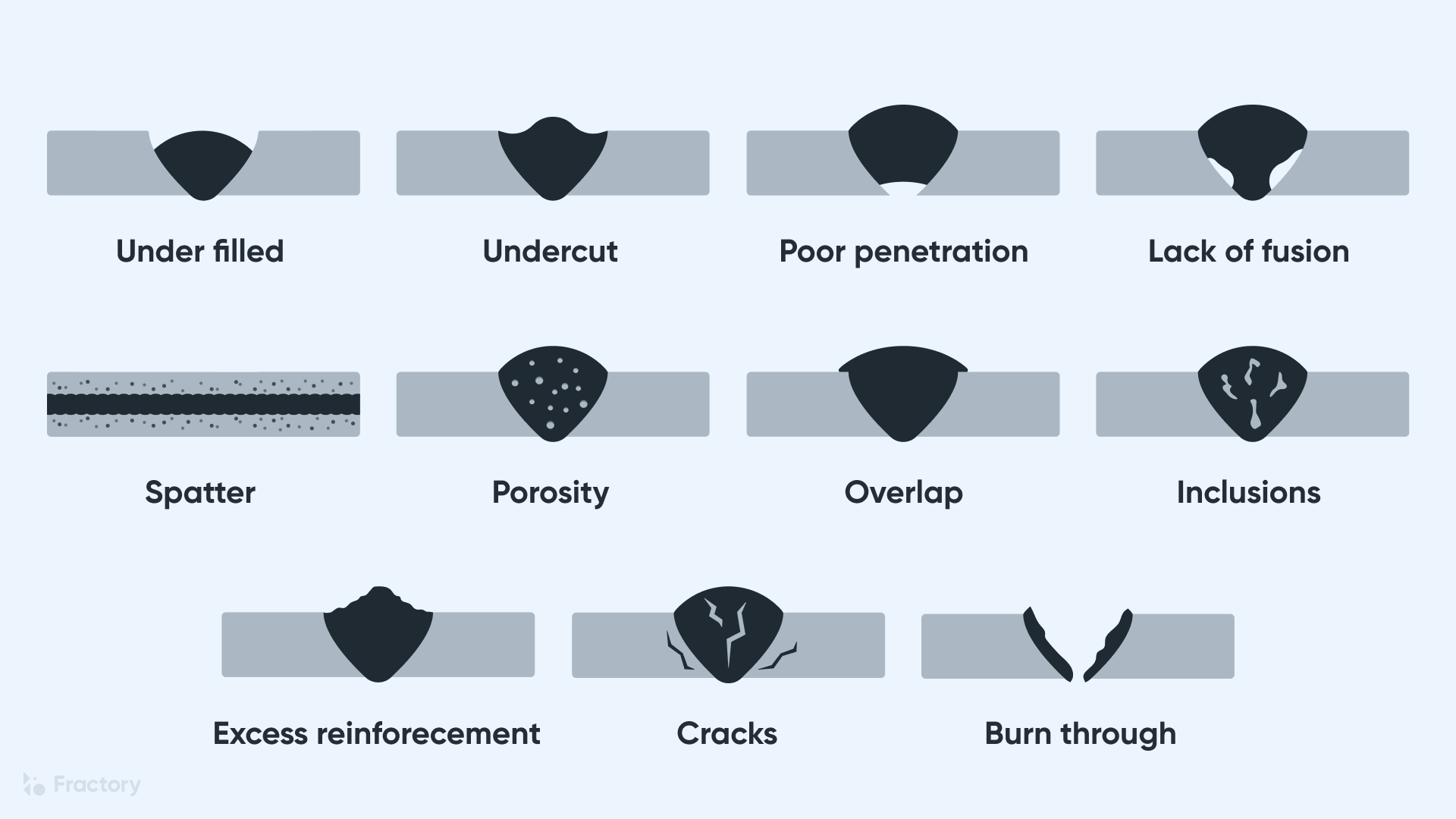
Examining and Quality Control Measures
Testing procedures are important to discover and avoid porosity in welding, making sure the stamina and sturdiness of the final product. Non-destructive testing methods such as ultrasonic screening, radiographic screening, and aesthetic assessment are frequently used to identify prospective issues like porosity.
Conducting pre-weld and post-weld assessments is likewise critical in keeping high quality control standards. Pre-weld examinations include validating the products, tools setups, and sanitation of the workspace to avoid contamination. Post-weld inspections, on the other hand, assess the final weld for any defects, including porosity, and verify that it meets defined standards. Carrying out a detailed quality assurance strategy that includes extensive testing procedures and inspections is paramount to reducing porosity concerns and making sure the overall high quality of bonded joints.
Verdict
Finally, porosity in welding can be a common concern that affects the quality of welds. By recognizing the typical sources of porosity and applying best practices for prevention, such as appropriate welding methods and testing procedures, welders can guarantee premium quality and trustworthy welds. It is necessary to focus on prevention approaches to reduce the event of porosity and preserve the stability of bonded structures.
Report this page